Technology & Service
Technical tips
Why true-peak detection is a better way for detecting bearing damage
Conventional vibration meter uses RMS (Root-Mean-Square) detection to measure vibration levels. The RMS value of a waveform f(t) is calculated by the following steps
- Convert the time waveform f(t) into waveform square f 2(t)
- Calculate the AREA under the waveform squared f 2(t)
- The square root of (Area divided by the time length T) is equal to the RMS value
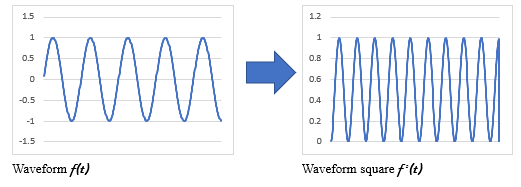
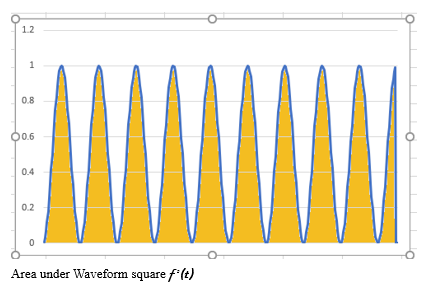
In addition to RMS detection, sometimes true-peak detection is also used to measuring the level of a time waveform. It measures the maximum value** of a waveform directly.
**Note: the waveform should be rectified first.
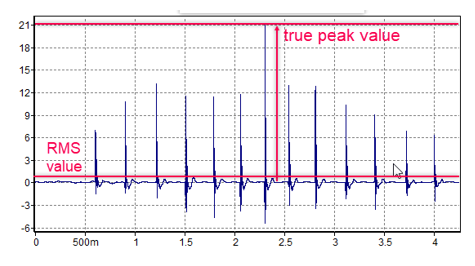
As a bearing starts developing defects, it generates periodic spike signals due to the metal-to-metal impact between parts. Because the duration as well as the area under the spike signal is very small, its RMS value is usually very small and ignored, too. At the beginning stage of bearing damage, RMS detection cannot reflect the bearing defect correctly, its value grows only when the damage achieves middle stage.
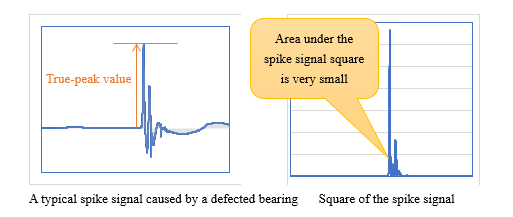
On the other hand, because true-peak detection measures the maximum value of a waveform, it can detect the bearing damage as the periodic knocking shows up at its early stage. Hence one can start tracking the trend of bearing damage from its early stage, (See the plot below)
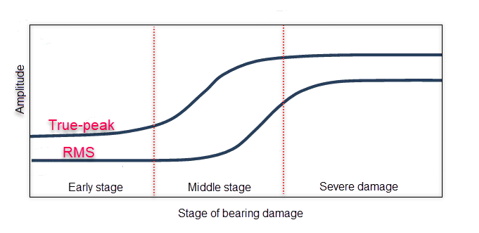
The true-peak detection also proves to be very effective for low speed or ultra-low speed machines. For machines rotates at or under 600 rpm, it is usually not easy to find out the bearing damage with a conventional vibration meter which utilizes RMS detection. The smart vibration meter vPod Pro, which adapts true-peak detection for measuring bearing condition, shows amazing results when measuring the bearings on 50 rpm ultra-low speed machines.